基于CAE技术的输液瓶盖模具设计及工艺参数优化
来源: 聚展网
2023-08-03 09:29:36
364
分类:
模具资讯
点击上方↑模具工业,吧
《模具工业》新的投稿系统正式上线啦!点击(模具工业 (cnki.net))在线办公系统中的作者投稿系统,注册后按提示操作就可投稿,欢迎投稿!
医用聚丙烯塑料具有高纯度、无毒害、无刺激性、化学稳定性好、不降解、不引起炎症、无过敏反应、生物相容性好、不致癌、不引起溶血和凝血等优点,并能经受环氧乙烷的消毒处理[2],此材料不仅力学性能较好,还具有优良的抗冲击性能和耐磨性,良好的尺寸稳定性和绝缘性[3]。医用输液瓶盖如图1所示,采用医用聚丙烯成型,最大径向尺寸为φ30.1 mm,高度为18.7 mm,塑件总体尺寸较小但产量大,结合模具零件加工、模架和成型设备的实际情况,采用1模20腔的注射模成型。塑件成型要在无菌化车间实现自动化的操作(不允许人工接触),模具采用点浇口进料,且点浇口凝料在开模后能自动脱落。塑件推出时不能产生较大变形和推出痕迹,因此不能设置推杆或推管推出,且②处需要强制脱模,再结合模具为1模20腔布局,成型塑件采用推件板推出。由于①处尺寸较小,为了保证塑件开模时留在动模且①处结构不损坏或变形,需要设置双向推出机构。综上所述,模具结构复杂,不能采用标准的三板模模架,需加工相应的专用模架。虽然塑件成型采用非标准模架,但依然可以参考标准的三板模模架,再加上注射模零件大多是标准件,因此,注射模设计主要包括成型零件设计、浇注系统设计、推出机构设计和冷却系统设计,现具体阐述各部分的设计。在成型工艺方案中,为了保证塑件开模后留在动模且①处(见图1)不变形或损坏,定模分开时要使定模型芯5先脱离定模型腔板4,由于采用推件板推出塑件,成型零件的结构采用图2所示的镶拼式结构。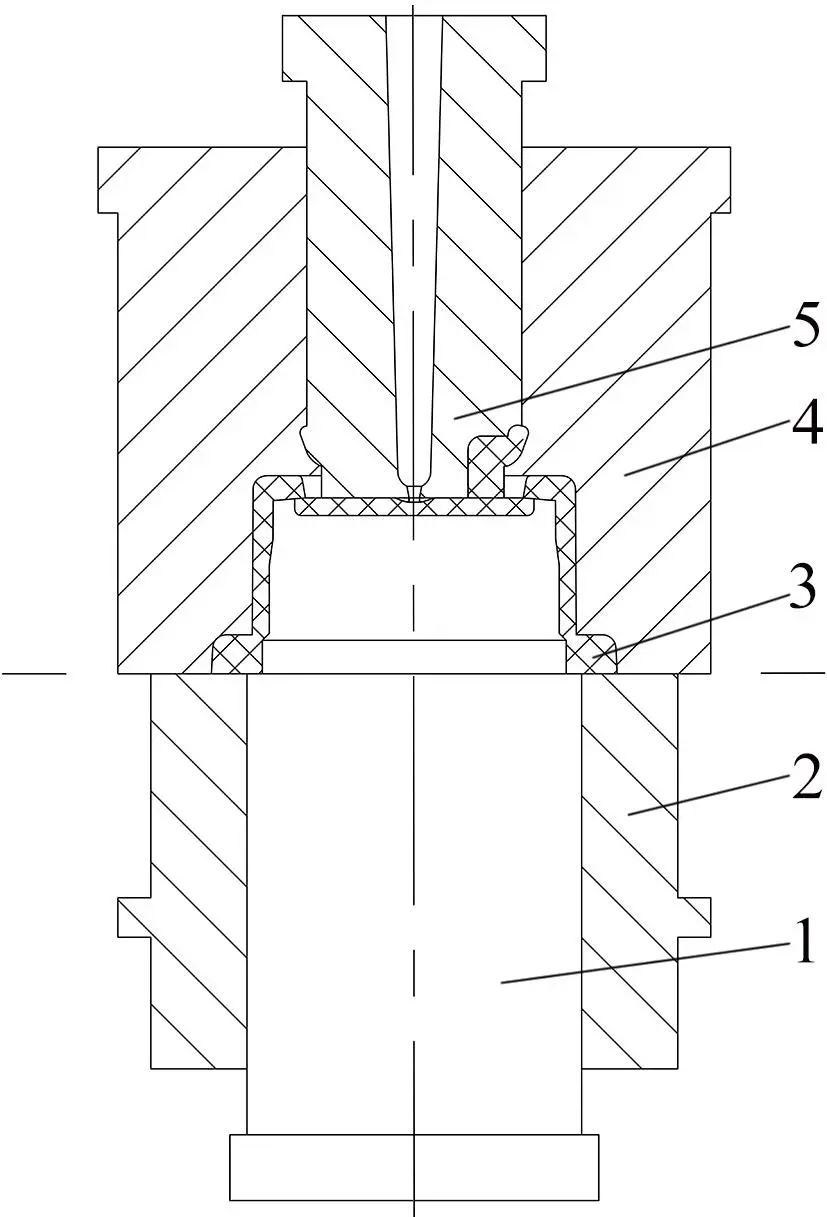
图2 成型零件结构1.动模型芯 2.动模型腔板 3.塑件4.定模型腔板 5.定模型芯
由于塑件是非对称结构,定模型芯、型腔板和动模型芯在安装时有方向要求,且都设有止转机构,再加上模具为1模20腔结构,综合考虑后,定模型芯、定模型腔板和动模型芯的定位装置如图3所示。为了实现自动化操作,模具采用点浇口进料,同时设置浇注系统的弹顶装置,如图4所示,定模分开后通过弹顶装置将流道凝料弹出模具外并自动脱落。为了缩短主流道的长度以减少废料,采用埋入式浇口套。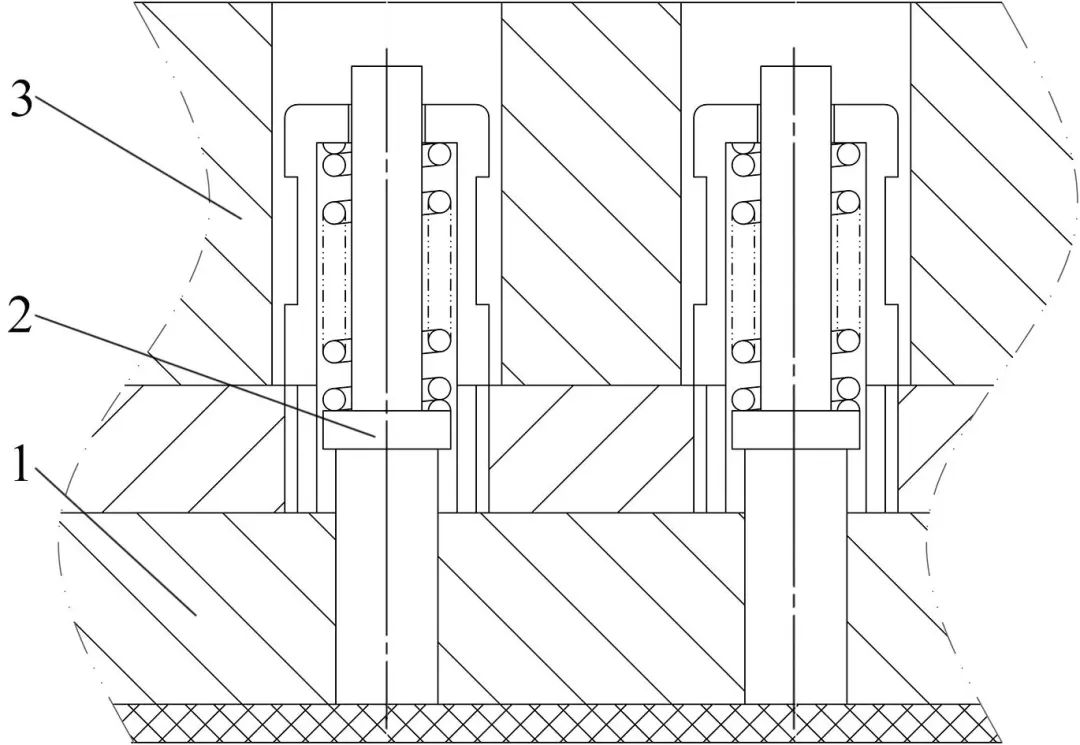
图4 浇注系统的弹顶装置模具采用推件板推出,为了保证塑件在开模时留在动模且塑件①处不损坏或变形,要使定模型芯在动、定模分开前先脱离定模型腔板,同时各分型面按照一定的顺序打开,因此采用双向推出机构和顺序分型机构。为了提高生产效率、缩短成型周期,保证各型腔中塑件收缩率的稳定性,需要在模具上开设冷却水道。冷却水道要便于加工且不能与其它零件产生干涉,需要在动、定模分别开设冷却水道,冷却水道的布局如图5所示。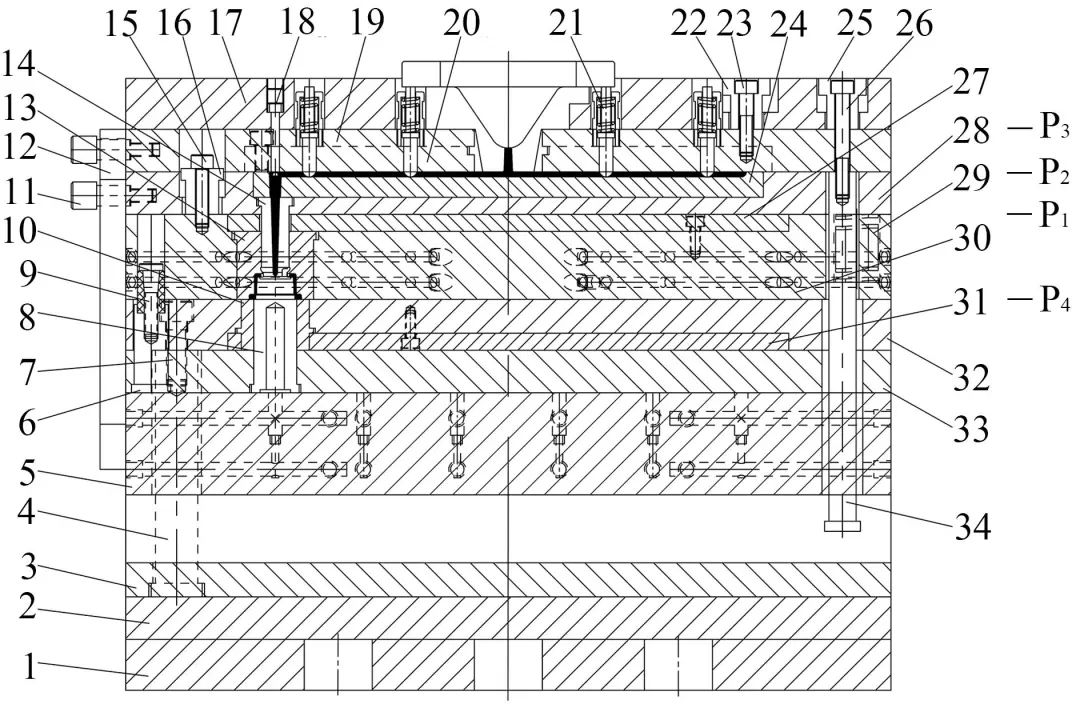
图5 模具结构1.动模座板 2.推板 3.推杆固定板 4.推杆 5.支承板 6.加长型固定柱 7.螺钉 8.动模型芯 9.圆形拉模扣 10.动模型腔板 11.螺钉 12.定距拉板 13.定模型腔板 14.定模型芯 15.螺钉 16.护套 17.定模座板 18.拉料杆 19.推件板 20.推件板垫板 21.弹顶装置 22.护套 23.螺钉 24.定模固定板垫板 25.推套 26.螺钉 27.定模板垫板 28.定模固定板 29.弹簧 30.定模板 31.推件板垫板 32.推件板 33.动模板 34.限位杆
由于温度、压力、时间等因素会导致塑件在成型时产生变形,须合理调整成型工艺参数,最大限度地减小塑件的变形量[4]。如果在试模时调整工艺参数,不仅浪费材料,且延长了试模时间,现采用Moldflow软件结合正交试验获得最优工艺参数,避免产生上述问题。将塑件模型以STL的格式导入Moldflow中,划分塑件网格并修改网格质量,复制塑件并建立浇注系统,最后建立冷却系统并划分网格,如图6所示。采用牌号为Escorene PP 9074的聚丙烯塑料,按照推荐模具温度范围20~80 ℃、冷却水温25 ℃、推荐熔体温度230 ℃、注射+保压+冷却时间默认、保压压力为最大充填压力(66 MPa)的80%进行冷却、填充、保压、翘曲的初始分析,塑件翘曲分析结果如图7所示,塑件总变形量为0.535 1 mm,由于收缩引起的变形量为0.470 4 mm,占塑件总变形量的87.9%,应从收缩不均方面进行优化。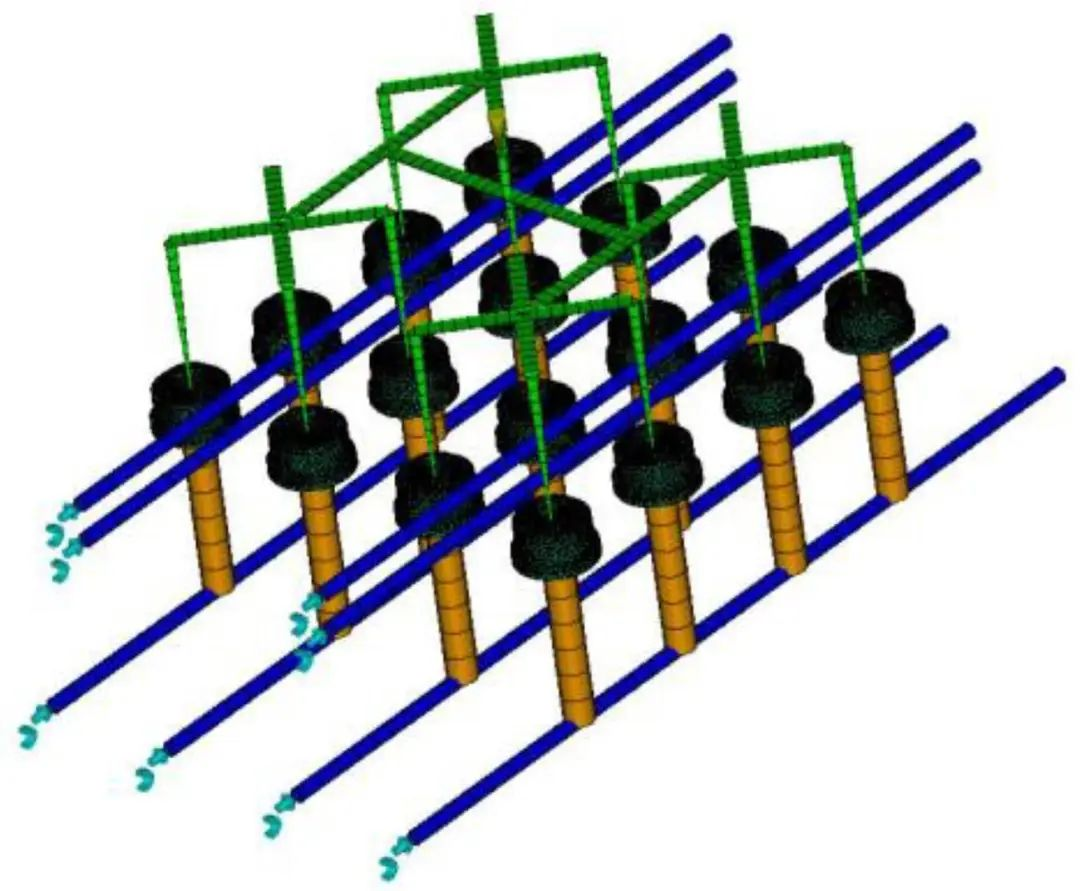
图6 模流分析模型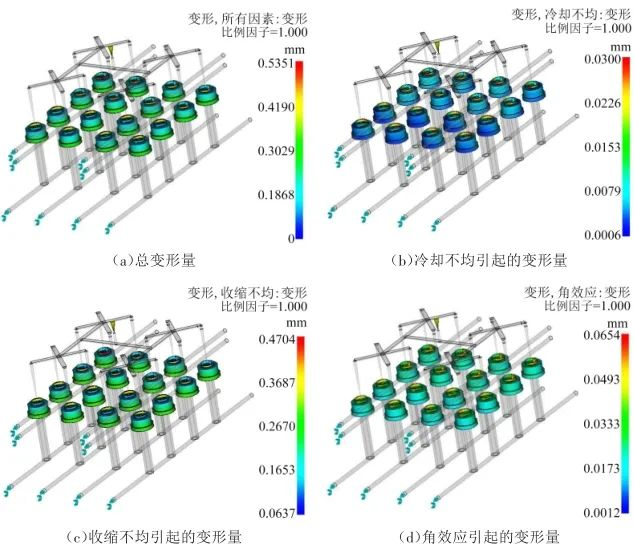
图7 塑件翘曲变形量
根据注射模设计相关知识及实践经验,采用Taguchi试验设计方法,选取对塑件变形影响较大的熔体温度、冷却水温度、保压压力、保压时间4个因素,每个因素取3个水平(各因素水平以能获得几何完整的塑件为前提),4个工艺参数因子的3水平选取如表1所示,试验以塑件总变形量S总、塑件收缩变形量S收缩为指标,且3个指标的数值越小越好,9次试验后结果如表2所示。对表2中S总、S收缩数据进行极差分析(见表3和表4)。由表3和表4可知,熔体温度A对塑件总变形量S总、收缩变量S收缩的影响最为显著。塑件总变形量S总的最优组合为A3B1C3D3;塑件收缩变形量S收缩的最优组合为A3B3C3D3。熔体温度与塑件总变形量S总、塑件收缩变形量S收缩的关系曲线分别如图8、图9所示。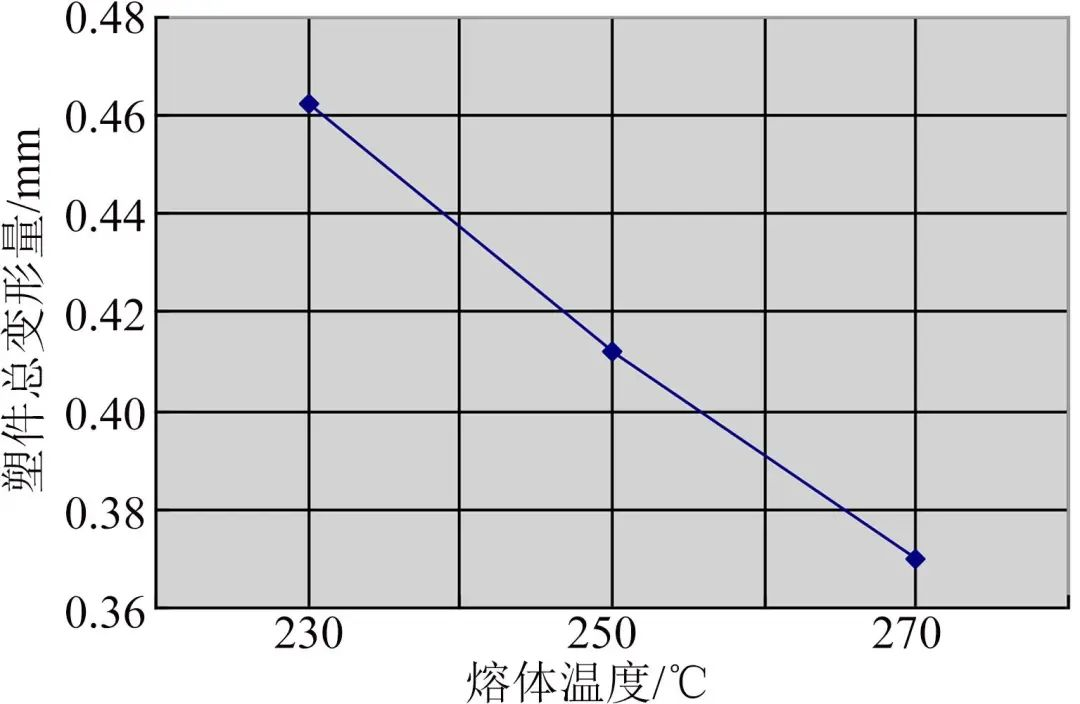
图8 熔体温度对塑件总变形量S总的影响
图9 熔体温度对塑件收缩变形量S收缩的影响对比S总、S收缩最优组合发现只有B1、B3不同,再结合表2得出因素2水平3的塑件的总变形量比因素2水平1的塑件的总变形量小。因此,成型参数的最优组合为A3B3C3D3,即熔体温度为270 ℃、冷却水温度为25 ℃、保压压力为最大充填压力的100%、保压时间为25 s。按照这个工艺条件在AMI平台上重新进行翘曲分析,得到的结果如图10、11所示,优化后的塑件总变形量比原先的小35%。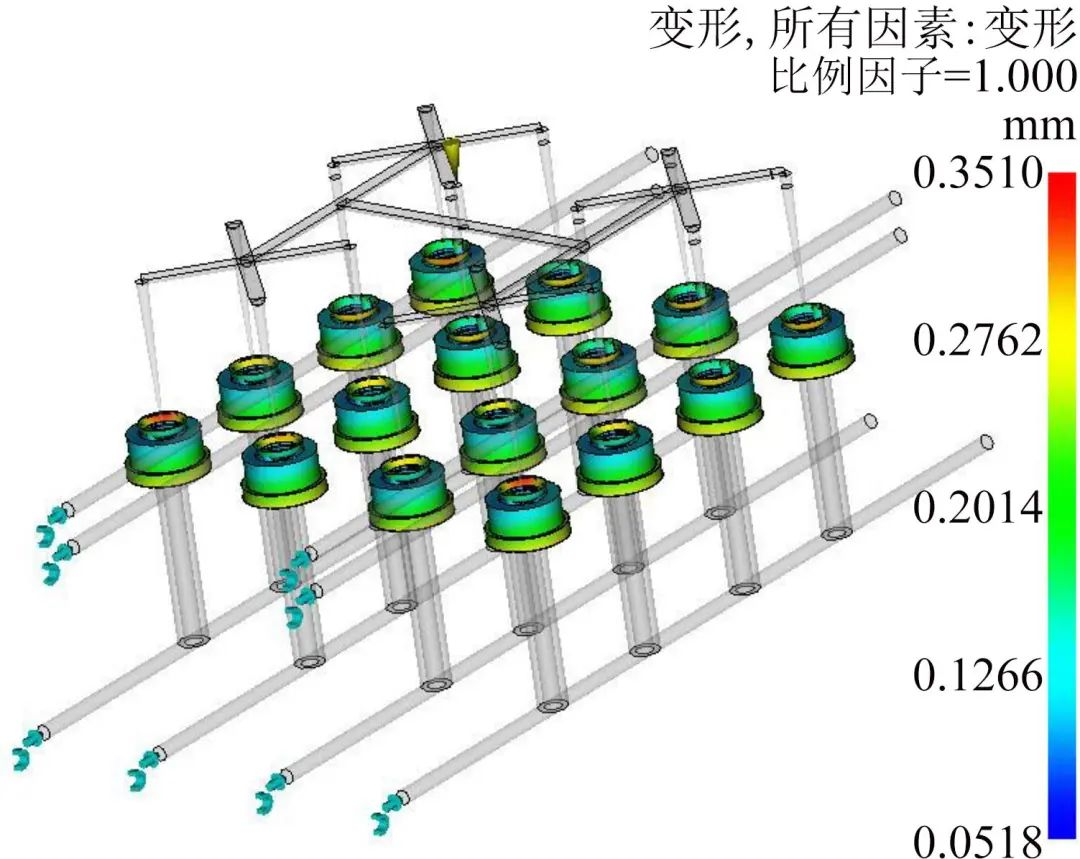
图10 塑件总变形量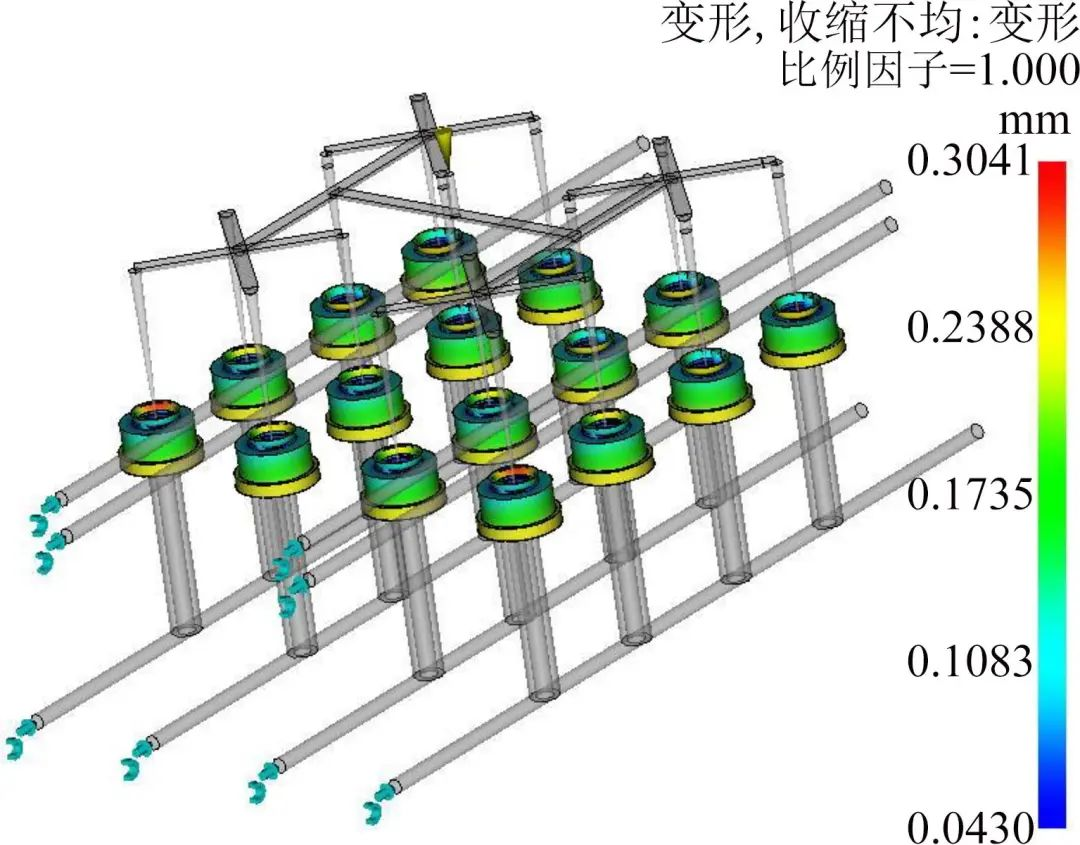
图11 塑件收缩变形量根据医用输液瓶盖塑件的要求和生产实际等情况,设计了注射模成型,采用Moldfolw软件对塑件进行初步模流分析,找出影响塑件变形的主要原因。通过对正交试验结果进行数值分析,得到塑件变形最小的最优成型工艺参数组合,缩短了试模周期、降低了生产成本,最终成型的塑件实物如图12所示,塑件变形较小,符合医用输液瓶盖的使用要求,说明模具设计合理。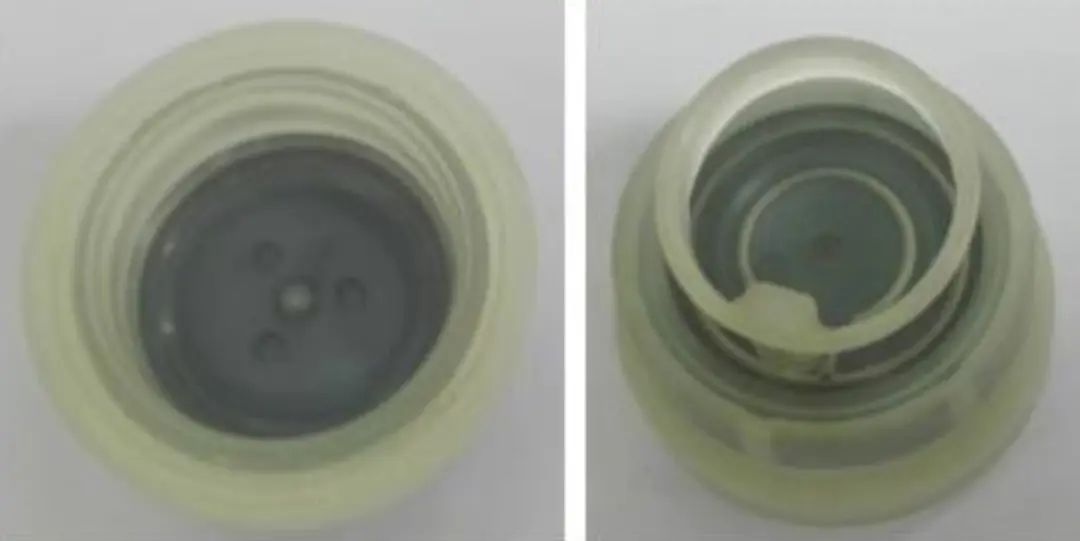
图12 医用聚丙烯输液瓶盖实物订阅杂志请加发行部QQ2762515535或致电0773-5861906垂询
声明:文章部分图文版权归原创作者所有,不做商业用途,如有侵权,请与我们联系删除。
来源:聚展网
点赞
分享:
2025.02.25-02.27
Asiamold
2024.10.02-10.04
METALEX Vietnam
2025.06.17-06.20
SheetMetal China
2025.05.21-05.23
MOULD EXPO
2025.06.18-06.21
INTERMOLD
2024.07.11-07.13
M'SIA-Plas
2024.11.26-11.29
DMP SHENZHEN
2025.06.17-06.20
Die&Tool China